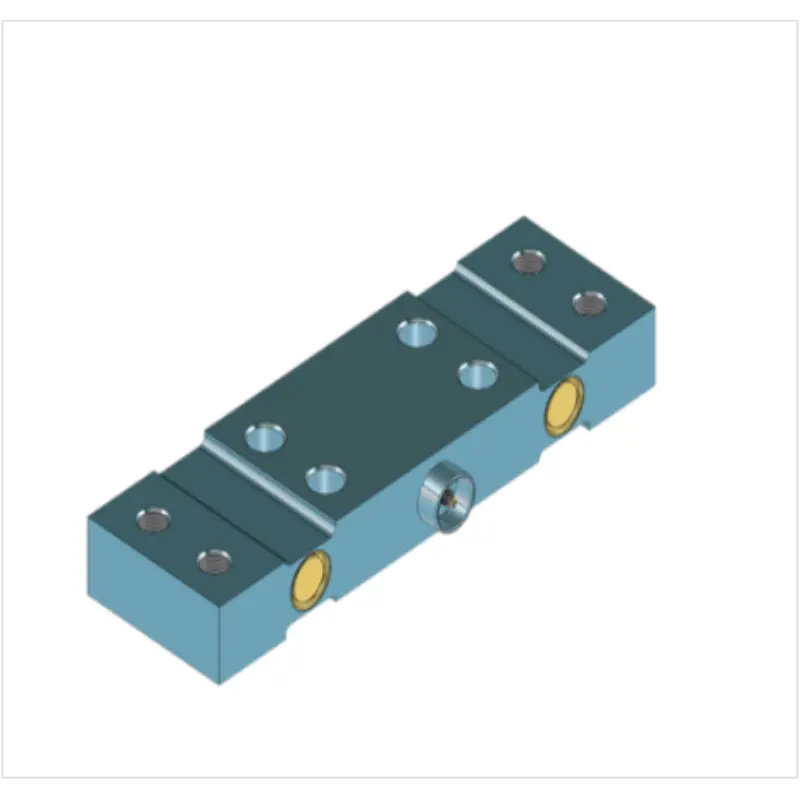
Bearing seat sensor / SMA41-WT Underwater bearing seat sensor
Product Categories Bearing seat sensor
The SM41 series bearing seat sensor is mainly installed under the bearing seat, and can also be used in other structural forms. It is a special sensor that mainly measures the bearing capacity of a bearing seat. The structural principle is a shear-type resistance strain sensor with fixed supports at both ends and a central load. High-quality alloy steel is selected as the elastomer and foil resistance strain gauge is used as the sensitive conversion element. The bearing seat is installed in the middle of the sensor, and the two ends of the sensor are fixed on the base. When the bearing seat is loaded, the load is transmitted to the base through the shear elastic beams at both ends, and a strain proportional to the load is generated in the elastic beam, which is converted into a corresponding electrical signal through the strain gauge. It is suitable for tension testing and control systems under bearing seats in various industries such as cranes and water conservancy.
1. Overview
The SM41 series bearing seat sensor is mainly installed under the bearing seat, and can also be used in other structural forms. It is a special sensor that mainly measures the bearing capacity of a bearing seat. The structural principle is a shear-type resistance strain sensor with fixed supports at both ends and a central load. High-quality alloy steel is selected as the elastomer and foil resistance strain gauge is used as the sensitive conversion element. The bearing seat is installed in the middle of the sensor, and the two ends of the sensor are fixed on the base. When the bearing seat is loaded, the load is transmitted to the base through the shear elastic beams at both ends, and a strain proportional to the load is generated in the elastic beam, which is converted into a corresponding electrical signal through the strain gauge.
It is suitable for tension testing and control systems under bearing seats in various industries such as cranes and water conservancy.
2. Features
- Strong anti-interference ability, easy installation and use, good stability.
- The flat plate shape makes the stress state stable, the lateral interference is good, and higher measurement accuracy can be obtained.
- Strong overload capacity, used for overload alarm of bridge crane.
- Fully sealed and waterproof design to meet all-weather use;
- High reliability;
- Easy and safe to operate;
3. Size
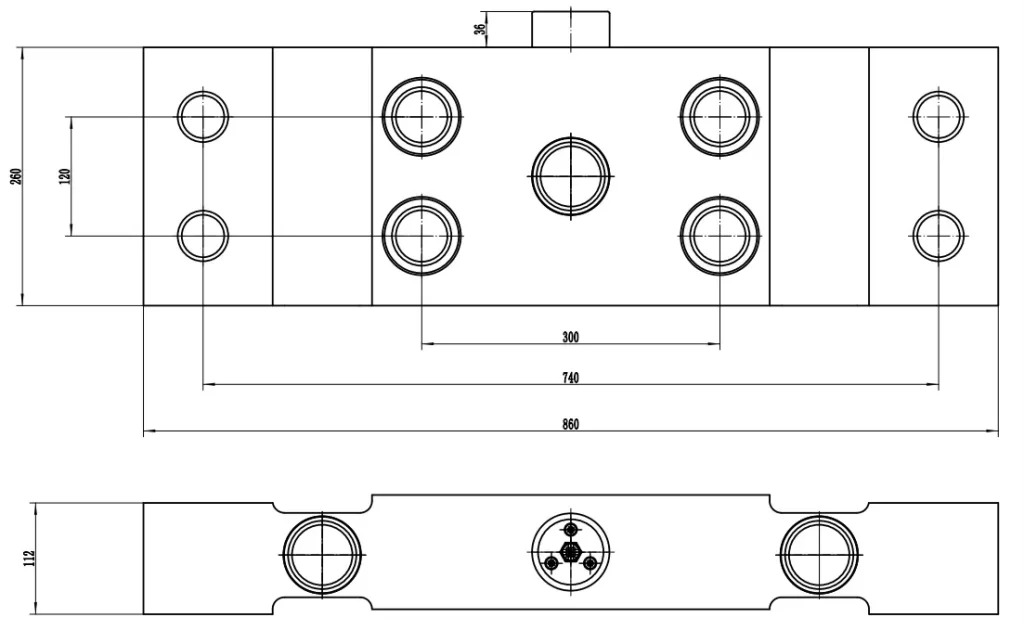
4. Main technical indicators:
Measuring range | 0~120T |
Rated load | 120T |
Safety load | 150% |
Limit load | 200% |
Operating temperature | -10~+70℃ |
Supply voltage | 24VDC |
Signal output | 4~20mA (dual-channel design) |
Material | 17-4PH (main material) |
Protection level | IP68 (200 meters underwater) |
Zero output | ±2% |
Zero drift | ±0.2%FS |
Comprehensive error | ±1% FS (non-linearity: ±0.75%FS; repeatability: ±0.3; hysteresis ±0.3%) |
Temperature influence on zero output | ±0.1%FS/10K |
Rated output temperature effect | ±0.1%FS/10K |
Long-term stability | ±1%FS/5 years |
Vibration test | Vibration resistance not less than 20g (EN60068-2-6, 5-500Hz, 10mm) |
5. Product Features
This product is mainly a special sensor for measuring the bearing capacity of a bearing seat. Its structural principle is a shear-type resistance strain sensor with fixed supports at both ends and a central load. High-quality stainless steel is selected as the elastomer and foil resistance strain gauge is used as the sensitive conversion element. The bearing seat is installed in the middle of the sensor, and the two ends of the sensor are fixed on the base. When the bearing seat is loaded, the load is transmitted to the base through the shear elastic beams at both ends, and a strain proportional to the load is generated in the elastic beam, which is converted into a corresponding electrical signal through the strain gauge. This sensor is fully sealed by argon arc welding to ensure its good sealing performance under 200 meters deep water. The rationality of its design is ensured by stress analysis of each point of the sensor.